Agricultural Processing
Full-Service Integrator of Control and Automation Systems for Process and Packaging.
Agricultural processing typically involves processing raw materials into agricultural products such as:
Human food consumables
Animal or plant food
Components/ingredients for other products
Using a fully integrated automation control system can increase
Efficiency
Safety
Consistency
Quality
Productivity
Agricultural processing needs a high level of automation and control over production due to:
Increased agricultural regulations
Demands for reduced headcounts
Need for consistency and quality control
As experts in a variety of custom agricultural processing systems, our engineers utilize the latest PLC, HMI and communications technologies to implement the most up-to-date control and automation system for your needs, improving your manufacturing productivity.
At Quantum Solutions, our experienced engineers provide control systems and automation integration to the world’s leading companies. We implement reliable, integrated systems that allow our clients to enjoy an optimal profit.

Examples of Custom Agricultural Processing Systems
Quantum Solutions built a custom automation system for a client in the Corn Processing Industry.
They needed to implement an automation system with the following features:
- Receiving product from semi-truck beds with hydraulic pumps and shaker containers
- Conveying corn
- Removing kernels from the ears
- Storing corn to be processed at another facility
A client in the Peanut Processing Industry needed to upgrade a 7-line system in order to improve quality, increase productivity, and allow the client to reduce headcount as necessary.
The solution included:
- Custom HMI & PLC code developed onsite while working directly with plant personnel to understand existing processes.
- Complete hardware migration
- Functionality reprogramming
- Operator training
- Centralized and line located HMI stations created
Quantum Solutions has helped a Flour Mill automate it’s previously fully manually-operated systems. The manual processes were causing a lot of system failures and backups, decreasing efficiencies and productivity. In order to increase productivity and efficiency while minimizing downtime, the client had to migrate their legacy systems.
This project included:
- Extensive preliminary engineering and documentation
- Multiple customer methodology reviews
- Inclusive functional description prior to programming
- Broad range of alarm notifications and OEE data to improve productivity, efficiency, and operator consistency
- Full graphic visibility of all equipment on a multi-terminal HMI system
- Full testing of all project facets to ensure effectiveness
Related Articles
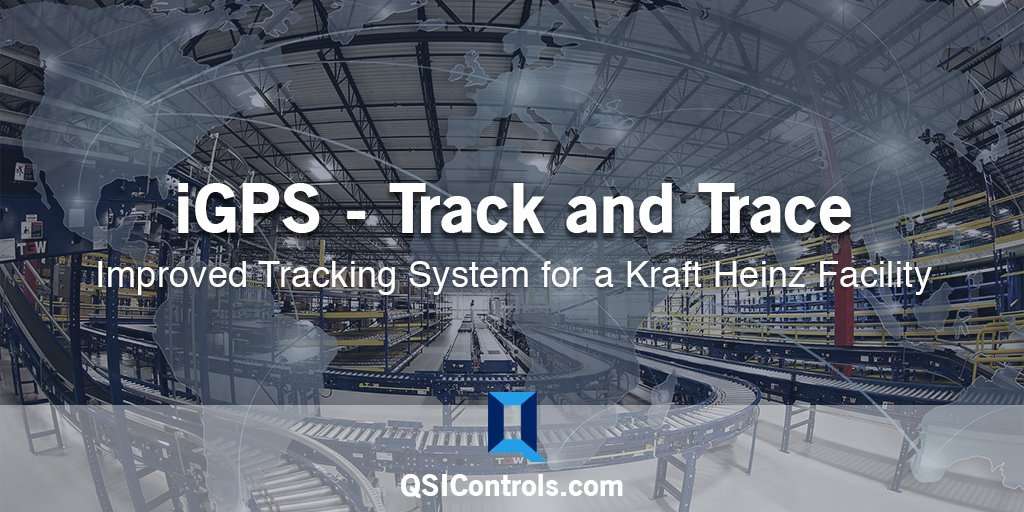
iGPS – Track and Trace Case Study
Today’s business world is increasingly complex; information, data, and communication are...
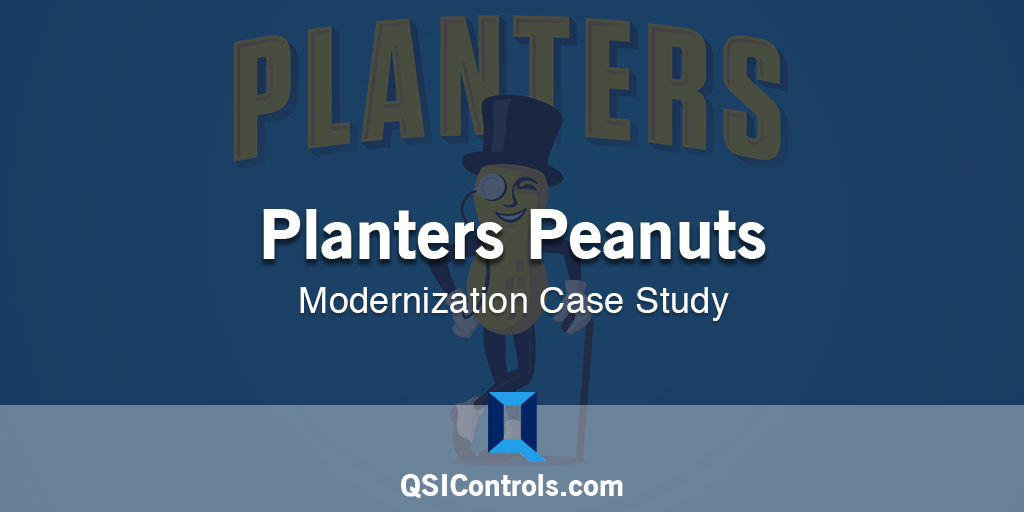
Hormel—Planters Peanuts: Cooker Lines Modernization Case Study
Quantum Solutions, Inc. (QSI) provided complete redesign, programming, commissioning, testing, and...
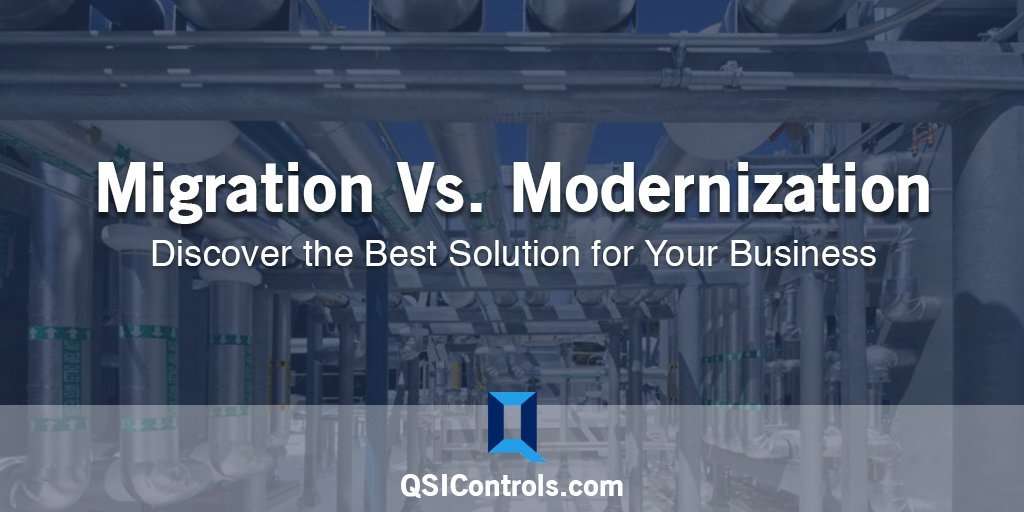
Controls Migration vs. Controls Modernization
Migration Versus Modernization for Process and Packaging Systems: What’s the Difference? The...